About SHANBEI technology
Focus on the development of Marine automation electronic equipment and systems
Ningbo SHANBEI Technology Co.,Ltd founded in April 2020, is a national high-tech enterprise founded by high-level talents in Ningbo City. The company has passed the quality management system certification of China Classification Society and is a member of China Ship and Ocean Engineering Industry Data Union. Since its inception, the company has focused on the development of Marine automation electronic equipment and systems.
Production situation
As a young Marine electronics technology company, in order to ensure that our products are processed using the latest production processes and manufacturing equipment, we choose to outsource part of the production of our products, which is also a common practice in the electronics manufacturing industry today, so as to ensure that our advanced product design can be realized and meet the highest quality standards. At the same time, we use in-house inspection and testing processes that meet the high requirements of the Marine industry, including stress and strain testing of key components and temperature testing to meet the harsh environment. To ensure the final quality consistency of our products, we design our own performance test devices and take additional quality assurance measures such as electromagnetic compatibility or UV exposure tests.
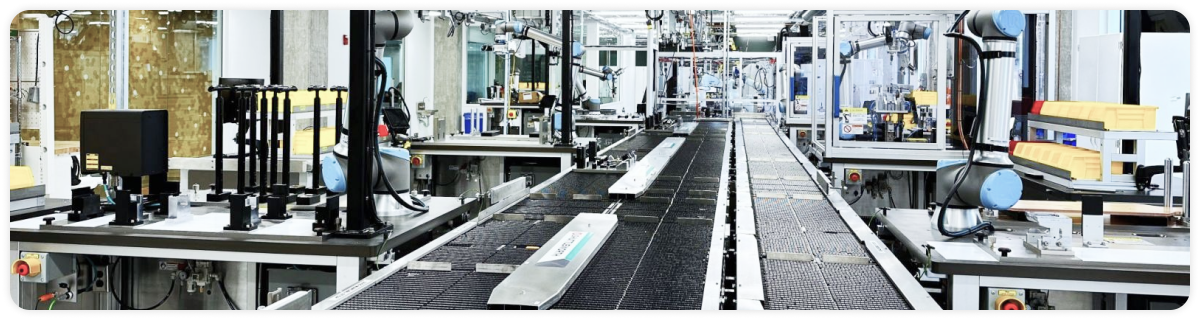
Our SMT machining
Surface Mounted Technology (SMT) production line for processing Surface Mounted Devices (SMD) on Printed Circuit Board (PCB), Leadless or short-lead SMD devices can be mounted on a printed circuit board or other substrate surface and then welded together by reflow or dip welding.All components required for SMT production, such as printed circuit boards (PCBS), surface mount devices (SMDS) and other small parts, are pre-stored in dry intelligent storage systems.
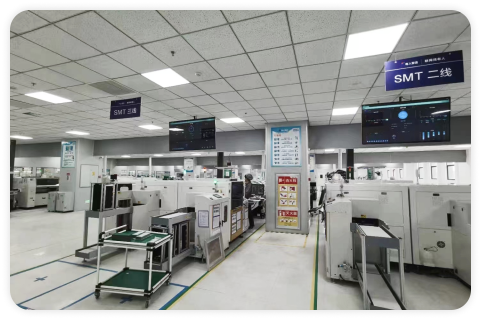
At the very front of the SMT line is the solder paste press, which is used to print solder paste or chip adhesive. The solder paste or chip adhesive can be deposited on the corresponding position of the pad or printed circuit board, and the thickness is consistent, so as to prepare for the installation of the component.Located behind the solder paste press on the SMT line, the mounter takes out the various SMD components and installs them exactly in the fixed position of the printed circuit board (PCB), placing 350 parts per minute with an accuracy of better than 1/100 mm.The reflow welder is located behind the SMT mounter in the SMT line and provides a stable heating environment to melt the solder paste pre-distributed on the PCB pad so that the SMD component and the PCB pad can be reliably bonded through the paste.
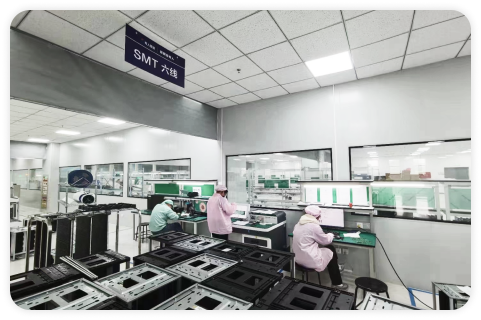
Our THT processing
THT (Through Hole Technology) is a technology that plugs components into the circuit board and then solds it with solder. THT uses leaded components, designs circuit connection wires and mounting holes on the printed board, inserts the component leads into the reserved through holes on the PCB, temporarily fixes them, and then welds them on the other side of the substrate to form reliable solder joints and establish long-term mechanical and electrical connections.As required, the leads of the components are semi-automatically measured and clipped and bent, and further processed on the preset bench, where the corresponding data of all THT components are recorded in the system and loaded onto the preset bench.
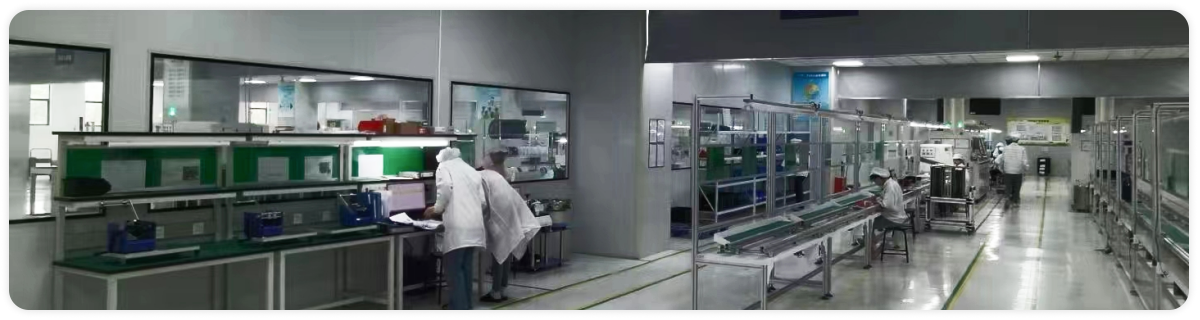
Our three prevention processing
For each product, we develop a tri-resistant coating process solution that reduces or eliminates the adverse effects of complex environments on electronic device performance. Through the three anti-processing, can achieve all aspects of insulation, moisture-proof, dust-proof, anti-corrosion and anti-mold, prevent the solder joint oxidation, prevent leakage, short circuit, beautiful appearance, bright.
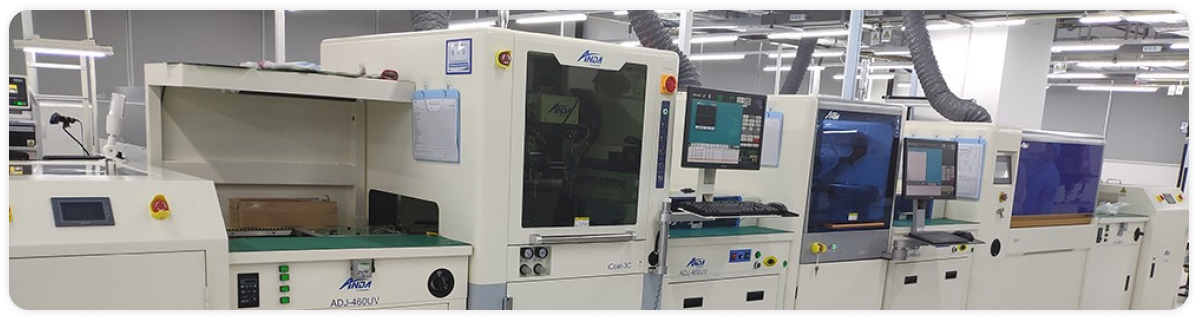
Our assembly process
Our whole machine products are assembled by many components, circuit boards, parts, shells, etc., must be assembled and connected in accordance with the design requirements in the specified position to form electronic products with specific functions. In addition to welding, we also use crimping, winding, gluing and other connection processes to meet the requirements of highly reliable connections.
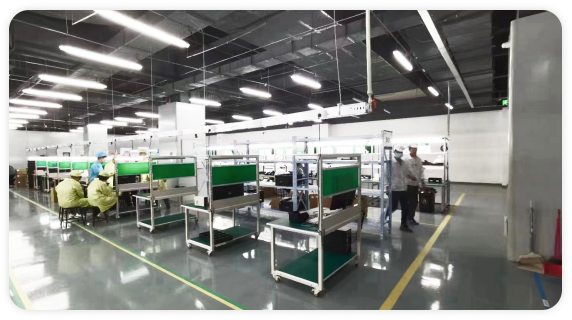
At all stages of the assembly process, we are equipped with optical error prevention devices to ensure that only the specified part storage box is opened for each process, so that the correct part is retrieved. The operator enters the next step after completing the operation confirmation through the foot switch, which minimizes the possibility of the whole machine assembly and ensures the consistency of the product.
